Factory Visit

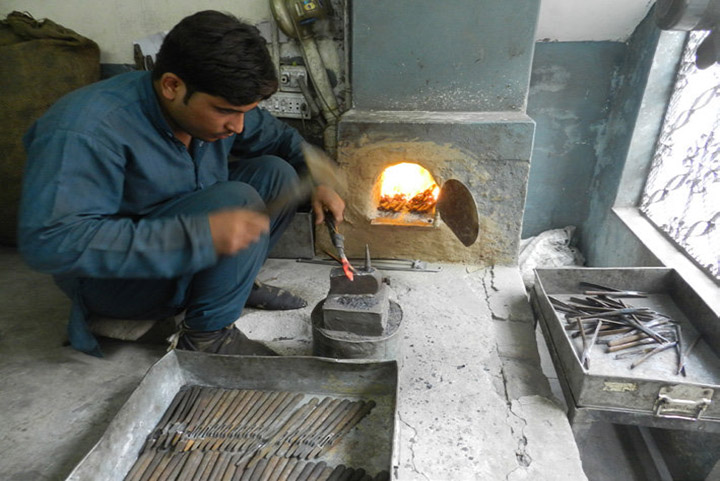
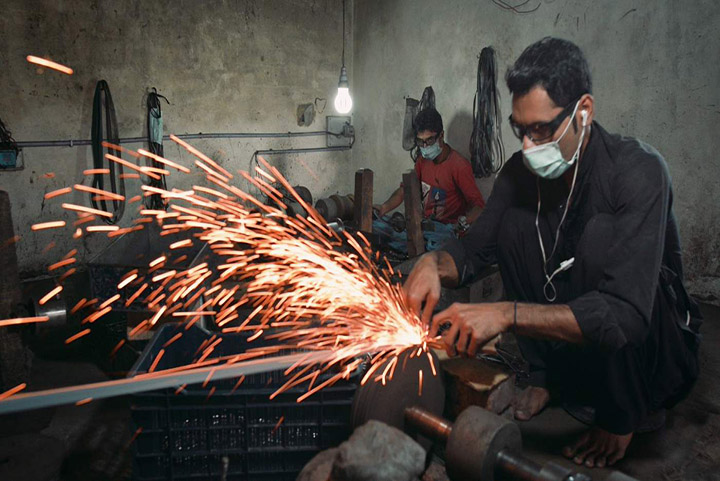
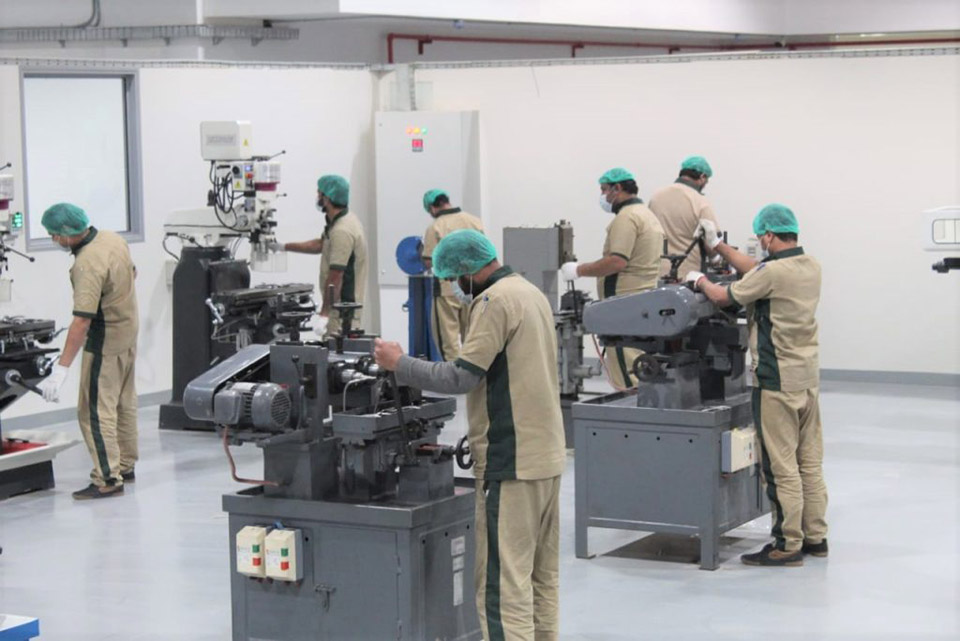
Process of Manufacturing
Initial Design
For new items, designs are drawn by hand or on a computer, often requiring input from surgeons, nurses, engineers, and other stakeholders.
Prototype
A 3D model is created by hand or computer, taking anywhere from a few hours to a few months, depending on complexity.
Raw Material Selection
Stainless steel, containing more than 11% chromium, is chosen for its corrosion resistance and self-repairing properties. Specific grades, like AISI 304, 410, 420A, and 420B, are selected based on application requirements such as hardness, flexibility, and tensile strength.
Die/Mold
A die or mold, either newly designed or based on an established pattern, is used for shaping materials, mainly through pressing.
Drop Forging
Metal parts are shaped through compressive forces in a hot or cold state. Hand forging is used for small orders, while hammer forging is for bulk quantities.
Press Work
Excess material is trimmed to refine the shape of the forged metal piece.
Surface Treatment
Techniques like pickling are used to clean the steel parts and enhance corrosion resistance by removing oxidation scale.
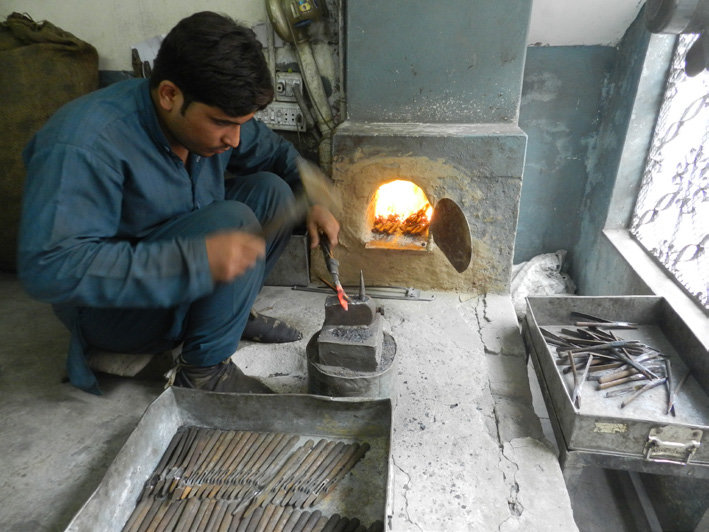
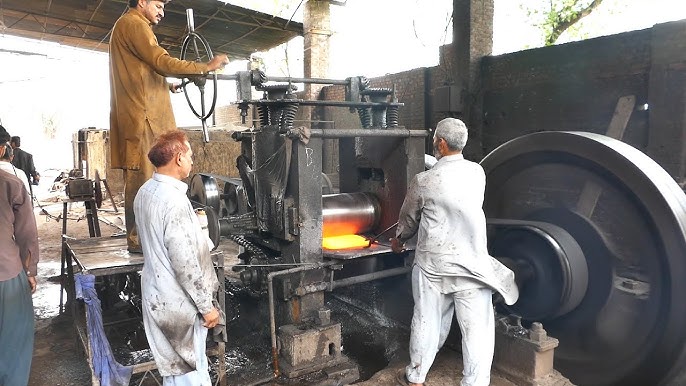
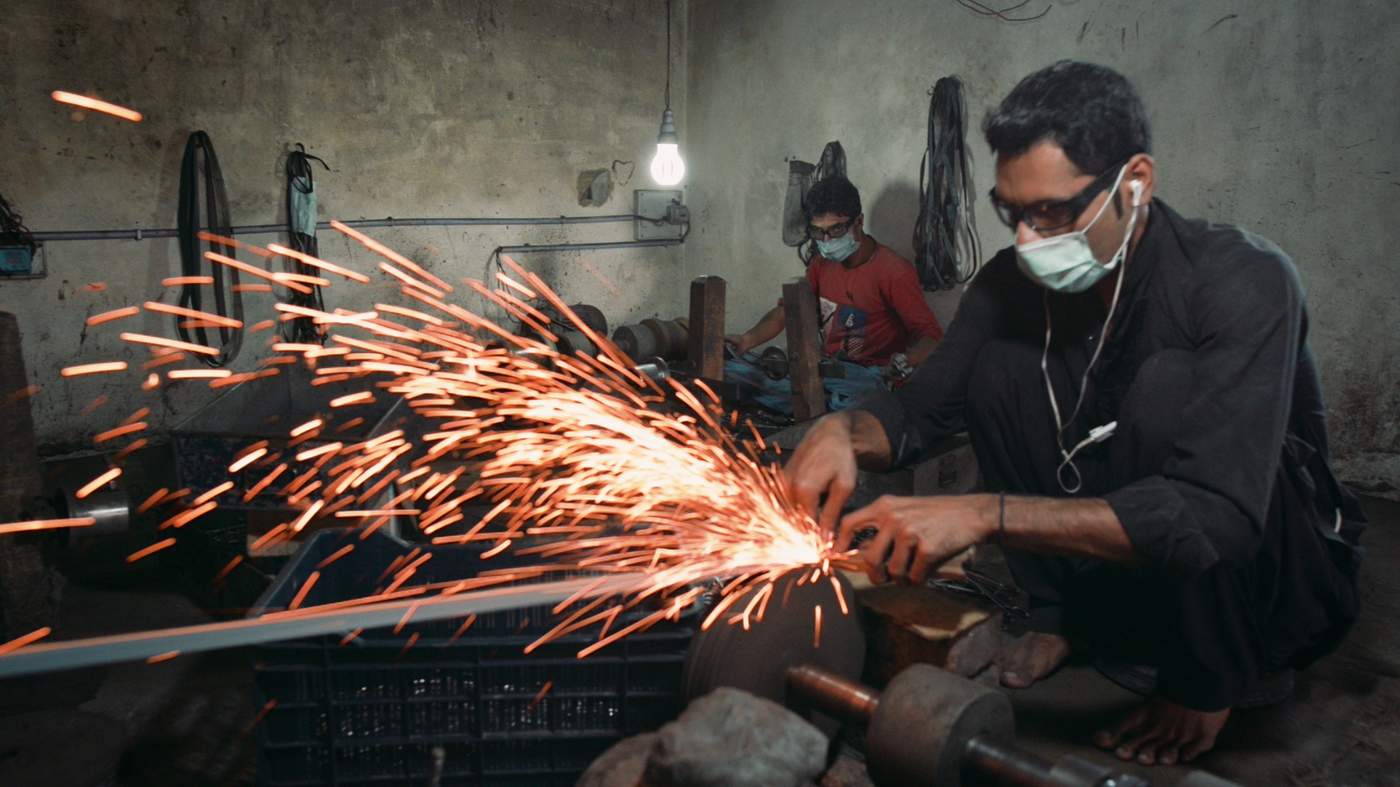
Machining
Material is removed using lathes, milling machines, and CNC machines to create specific features such as serrations, grooves, and joints.
Filing
Grinding wheels and files are used to further refine the shape, ensuring the general form and initial settings are accurate.
Injection Molding
Complex and precision-shaped parts are produced from various materials without machining, offering superior strength and surface finish.
Heat Treatment
Processes like annealing (softening), hardening, and tempering (toughness) are used to alter the physical and mechanical properties of the instruments.
Electropolishing
An electrochemical process that enhances the surface passivity, brightness, and smoothness of the metal, also removing some burrs.
Polishing and Buffing
Metal finishing processes to achieve desired appearances, such as a mirror or dull finish, using abrasives on a rotary wheel.
Ultrasonic Cleaning
Ultrasound is used to remove any foreign matter, such as polish or metal bits, from the instruments.
Functional Setting and Testing
Instruments are aligned and tested to ensure proper functionality.
Color/Powder Coatings
Coatings such as gold, black, or titanium are applied for additional protection and aesthetic purposes.
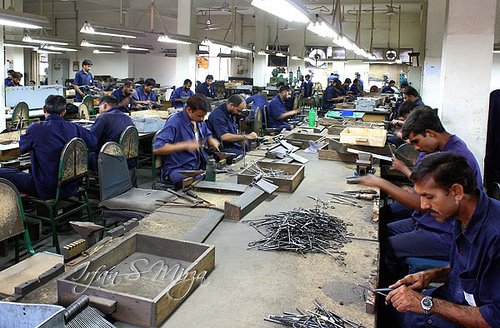
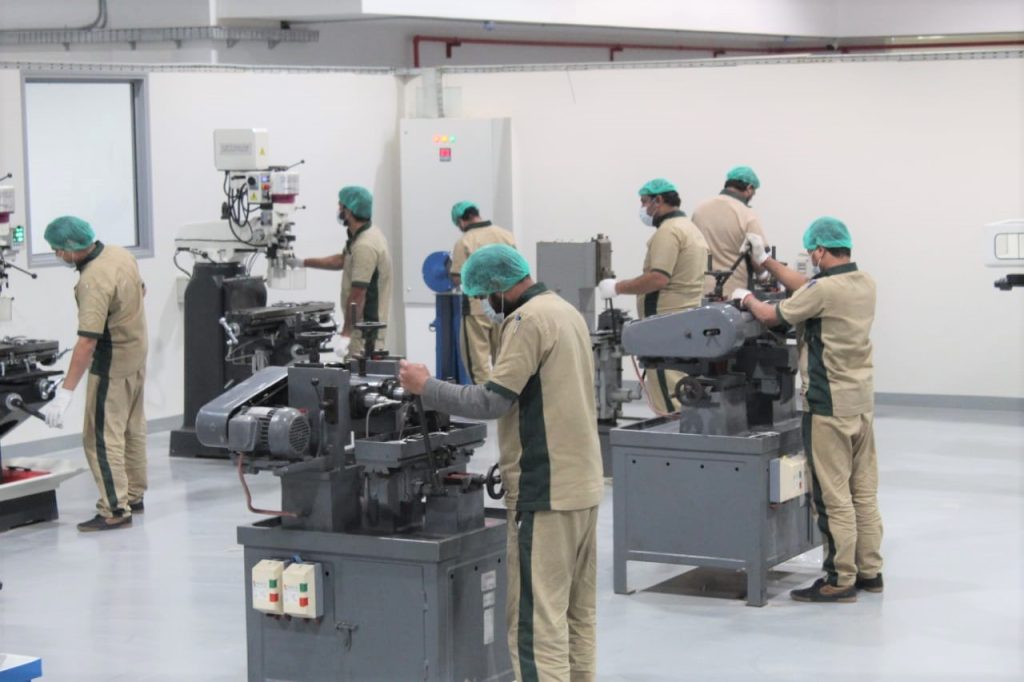
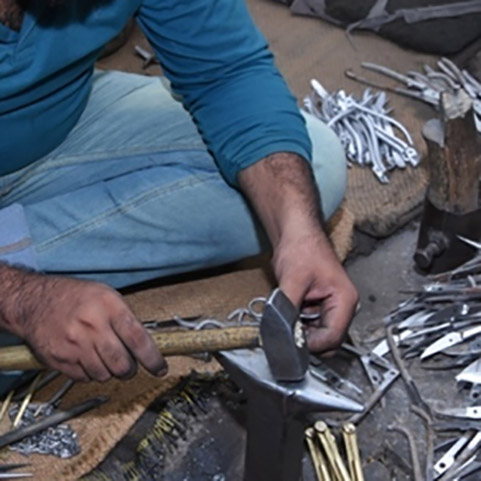
Passivation
Stainless steel instruments are immersed in nitric or citric acid solutions to remove impurities and restore corrosion resistance.
Oiling
Instruments are oiled to maintain smooth operation.
Quality Checking
A thorough inspection ensures the instruments meet quality standards, focusing on the final finishing which is crucial for reliability and performances
Packing
Good packing ensures the surgical instruments are protected from contamination and damage, maintaining their sterility and functionality until use. It typically involves sterile, tamper-evident packaging materials and careful handling to preserve instrument integrity
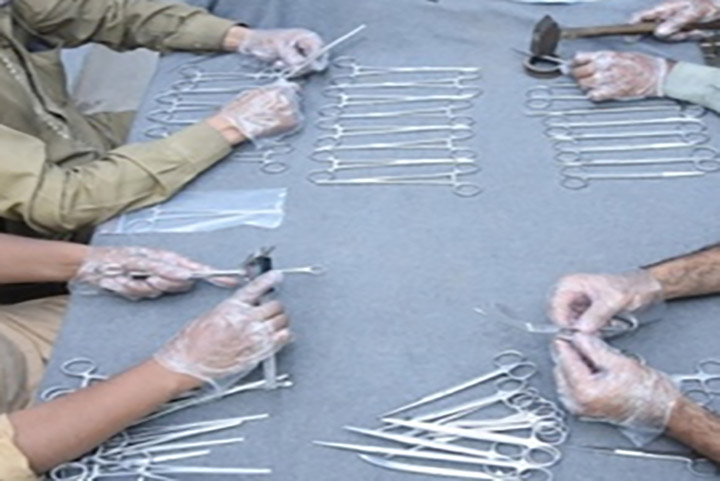
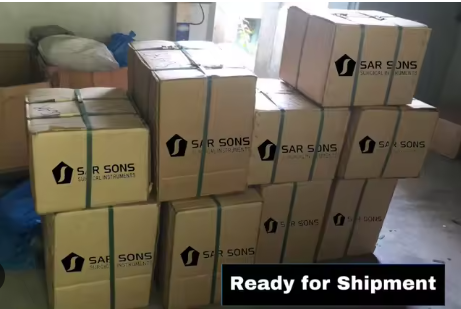